M3D
Im Zuge des M3D Projekts wird die gesamte Prozesskette von der mobilen 3D-Erfassung bis hin zum 3D-Druck in einem industriellen Umfeld mit dem Ziel untersucht, das enorme Potential von ortsunabhängigen Mobilgeräten und Clouds zu analysieren und Technologien zu optimieren. M3D ist das neueste vom Bundeministerium für Wirtschaft und Energie (BMWi) geförderte Projekt.

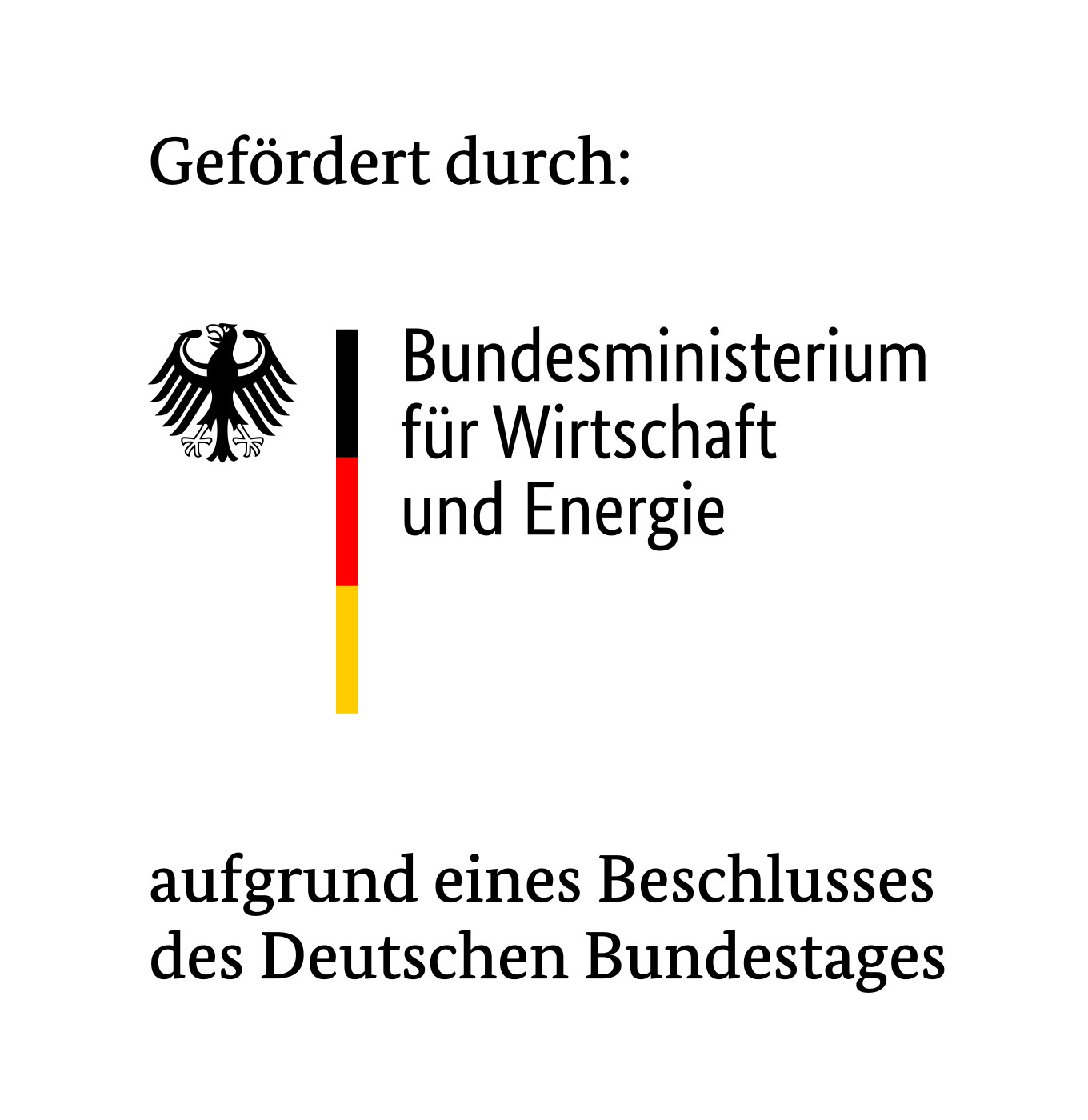

Projektdetails
M3D beschreibt ein laufendes Kollaborationsprojekt verschiedener Partner zur Mobilen 3D-Erfassung und 3D-Druck für industrielle Anwendungen. Die immer weiter steigende Geschwindigkeit in der digitalen Datenübertragung hat dazu geführt, dass die Erzeugung, Verarbeitung und Darbietung von Audio- und Videodaten sowie multimedialen Dokumenten aller Art ortsunabhängig geworden sind. Die ebenfalls rasante Entwicklung von Ein- und Ausgabetechnik für 3D-Daten wird diese Ortsunabhängigkeit in der Erfassung, Verarbeitung und Erzeugung auch für reale 3D-Objekte bzw. Produkte ermöglichen. Ein besonders wichtiger Aspekt ist in diesem Zusammenhang auch die rapide Entwicklung bei additiven Fertigungsverfahren, die medial gerade unter dem Begriff 3D-Drucker bekannt werden.
Während diese Technologien bisher meist industriell zur Herstellung von Prototypenteile verwendet wurden, zielen neue Anwendungen auf die Fertigung von Produkten sowie Produkt- und Ersatzteilen. Hierzu laufen zahlreiche Aktionen durch Prozessoptimierung die Bauteilqualität zu erhöhen, so dass in wenigen Jahren ein Einsatz für viele Produktteile wirtschaftlich möglich sein wird, solange sehr kleine Losgrößen oder Kleinteile benötigt werden. Dies ist besonders in der Ersatzteilebeschaffung der Fall. Es fehlt aber ein Prozess zur schnellen und preisgünstigen Beschaffung von fertigungsgerechten 3D-Daten. Dieser Prozess kann in Zukunft aber in vielen Anwendungsfällen durch die Möglichkeit einer mobilen 3D-Erfassung unterstützt, vereinfacht und beschleunigt werden.
Im Projekt soll das enorme Potential dieser Entwicklungen am Beispiel von Bauteilen und Werkstücken in industriellen Anwendungen konzeptionell und technologisch untersucht und in prototypischer Form demonstriert werden. Dazu sollen mit mobilen Endgeräten vor Ort notwendige Bauteile erfasst oder vermessen, diese in Bauteildatenbanken identifiziert und mit vorhandenen Modelldaten abgeglichen werden. Ein komplett digitaler Prozessablauf ermöglicht vor der Erstellung mittels additiver Fertigung eine Modellsimulation um mögliche Schwachstellen im Bauteil zu identifizieren und vor der Herstellung zu beheben. Dabei profitieren alle Schritte von der Anbindung aller Geräten über schnelle Datenkommunikationsnetze an dezentrale Speicher- und Rechenanlagen (die sog. „Cloud“).
Abbildung 1: Skizzenhafter Überblick des vorgesehenen Arbeitsablaufs für die mobile Erfassung, verteilte Verarbeitung und additive Fertigung von Objekten
Am Beispiel von Bauteilen und Werkstücken in industriellen Anwendungen wird das Potential konzeptionell und technologisch untersucht und in prototypischer Form demonstriert. Das Projekt besitzt im Wesentlichen fünf Hauptarbeitsziele:
- Entwicklung neuer bild- und sensorbasierte Algorithmen zur 3D-Datenerfassung
- Entwicklung von Verfahren und Algorithmen zum Datenmanagement und zur Identifikation
- Entwicklung von Verfahren zur Datenverarbeitung für die additive Fertigung
- Entwicklung von Technik zur cloudbasierten Unterstützung einer schnellen, echtzeitfähigen 3D-Datenverarbeitung
- Aufbau eines Demonstrators zur Erprobung der entwickelten Technologien
M3D Abschlussprojektpräsentation, 29. November 2018
Um die Resultate des im November 2018 zu Ende gegangen M3D-Projekts der Öffentlichkeit zu präsentieren, veranstaltete das 3IT eine Ergebnisse zusammenfassende M3D-Abschlusspräsentation.
Der Workshop bestand aus sieben Präsentationen, die einen Überblick über die wichtigsten Forschungsaktivitäten und die erzielten Ergebnisse gaben, darunter eine Ausstellung mit fünf Demonstratoren, die von den Projektpartnern während der Projektlaufzeit entwickelt wurden.
Folgende Präsentationen stehen zum Download bereit:
“Mobiles System zur Aufnahme und Rekonstruktion von Bauteilen” von Eric Wisotzky, Fraunhofer HHI
“Bauteile auf Basis von CAD- und Rekonstruktionsdaten für die additive Fertigung effizient simulativ prüfen” von Tim Grasser, Fraunhofer IGD
“Beschädigte Bauteile auf Basis präziser (teil-)automatisierter Scanmethoden rekonstruieren” von Thomas Lück, cirp
“Hardware-beschleunigtes Cloud-Computing für die Bauteile-Identikifaktion” von Christian Unger, CPU 24/7
Bild- und sensorbasierte Algorithmen zur 3D-Datenerfassung
Die digitale Erfassung der Objektdaten erfolgt auf zwei verschieden Wegen. Zum einen mittels Fotos durch ein mobiles Endgerät (photogrammetrisch) und zum anderen mittels Streifenlichtscanner (siehe Abbildung 2). Die Herausforderung bei beiden Verfahren zur Aufnahme von Industrieobjekten sind transparente, homogene, dunkle absorbierende und/oder reflektierende Materialien und Oberflächen welche eine robuste Datenakquise erschweren. Filter und spezielle Algorithmen führen zu ersten dünnbesetzen Punktwolken welche mittels einem erweiterten Poisson-Meshing in ein verfeinertes 3D-Objekt überführt werden können, siehe Abb. 3. Dieses soll nun durch Nutzerinformationen verbessert werden.
Datenverarbeitung für die additive Fertigung
Um ein verbessertes Objekt als Ersatzteil in den Einsatz zu bringen erfolgt vor der additiven Fertigung eine umfangreiche Simulation verschiedenster Anwendungen am digitalen Objekt, um vorangegangene Defekte zu vermeiden. Eine Lastfallanalyse mittels der Finite-Elemente-Methode gibt einen Aufschluss über mögliche Bruchstellen des Objektes (Abb. 4) und lässt eine Optimierung des Modells zu. Anhand dieser Informationen kann eine Form-Optimierung erfolgen.

Eine anschließende geometrische und physikalische Optimierung des Modells erlaubt eine optimale Modellierung für die additive Fertigung. Somit wird es möglich sein, die Artefakte welche durch das, in der additiven Fertigung nötige, Slicing entstehen zu minimieren und die Herstellungszeit ebenfalls zu minimieren, bzw. zumindest konstant zu halten.
Das Projekt gliedert sich in verschiedene Arbeitspakete (AP 1 – AP 5), die sich den einzelnen Schritten in der Prozesskette widmen. Die Projektpartner widmen sich mit ihrem speziellen Fachwissen unterschiedlichen Arbeitspaketen und tragen die Ergebnisse dann zusammen.
AP1: Projektleitung
AP2: Anforderungen und Systemarchitektur
AP3: Mobile 3D-Erfassung und 3D-Rekonstruktion
AP4: Datenmanagement und Algorithmen zur Identifikation
AP5: Modellierung von Daten für additive Fertigung
AP6: Hardwarebeschleunigte Serverarchitektur für Cloud Processing
AP7: Integration & Demonstratoraufbau
M3D Projekt-Abschluspräsentation
29. November 2018
Location: 3IT Berlin
Details und Registrierung: https://www.3it-berlin.de/events/m3d-completion/
CAxMan-Roadtour: Finaler Stopp in Darmstadt
28. August 2018
Der Workshop war einer von fünf internationalen Workshops, die vom EU-finanzierten CAxMan-Projekt (Computer-Aided Technologies for Additive Manufacturing) in fünf verschiedenen europäischen Ländern organisiert wurden und fand am 28. August 2018 am Fraunhofer IGD in Darmstadt statt.
CAxMan ist ein Forschungs- und Innovationsprojekt für cloudbasierte Toolboxen, Workflows und ein One-Stop-Shop für computergestütztes Design, Simulation und Prozessplanung in der additiven Fertigung.
Prof. Dr. Philipp Urban, Leiter der Abteilung “3D-Drucktechnologie” des Projektpartners Fraunhofer IGD, präsentierte die wichtigsten multimateriellen 3D-Drucktechnologien der Branche.
Neben den informationstechnischen Herausforderungen bei der Steuerung der Maschinen wurde der ebenfalls am Fraunhofer IGD entwickelte strömungsfähige, voxelbasierte 3D-Druckertreiber “Cuttlefish” am Beispiel des grafischen Multimaterial-3D-Drucks vorgestellt.
Ein weiterer Referent war Thomas Lück vom Projektpartner cirp mit seinem Vortrag “Industrial Requirements for Additive Manufacturing”.
3IT Summit: Meilensteinpräsention des Projekts
23.10. & 24.10.2017
Hier finden Sie den Vortrag von cirp GmbH zum Download.
FormNext: internationale Ausstellung und Konferenz zum Thema neuer Fertigungstechnologien.
Moulding Expo 2017 Stuttgart: Molding Expo 2017 Stuttgart: